HOME
BADGES
TROPHIES
ENGRAVING
SEARCH
SITE MAP
CONTACT US
POLICY
|
SEAL PRESSES
High quality seal presses. All artwork, engraving of the
dies and setting up of the press can be done on our premises by our skilled
tradesmen. The sample shown here is a very simple but common design
for a seal press, but there are many other options... Crests, Coat of Arms,
Logos, Documents, Certificates, Photographs, Addresses, Envelopes, Letterheads,
Incorporated Societies, Companies, Re-Unions, Legal or Domestic.
When ordering please specify if to be used at the top or the bottom of
the document.
Artwork... As used in the
Moller & Young Sample - 35mm
Let us design your seal to suit your requirements.
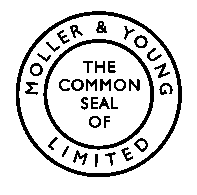 |
Vinyl Seals - Moller & Young Vinyl Seals are
made from a high quality mouldable vinyl and supplied
with contact adhesive on the back.
Sizes available in stock...
SEA50 (50mm
round)
SEA68x39 (oval)
SEA70 (70mm
round)
SEA70x45 (oval)190mm |
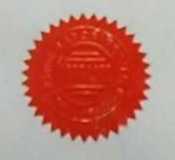 |
Dies... A matching ‘Male & Female’ set of
dies as used in the Moller & Young Sample and fitted into the SPS
small press. |
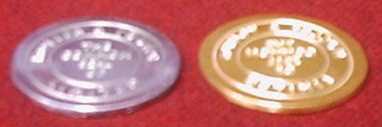 |
SPL Large Press
Die Size: 45mm
Seal Size: Maximum 38mm
Leverage: 60:1
We recommend using this press when fine detail is required
in the ‘Seal’ or the paper/vinyl used is thicker or harder than standard
copier paper.
It may also be used for any seal where a heavier machine
is preferred. |
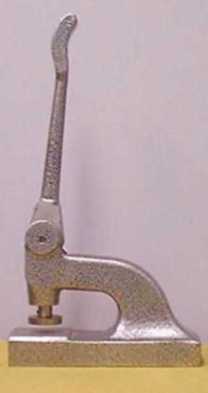 |
SPM Medium Press
Die Size: 38mm
Seal Size: Maximum 25mm
Leverage: 16:1 |
SPS Small Press
Die size: 43mm
Seal Size: Maximum 35mm
Leverage: 13:1
We recommend using this press when the equivalent of
standard 80gsm copier paper and Moller & Young vinyl seals are used
and the embossing required is simple and bold as with the Moller &
Young sample shown. |
Directions for Embossing - Moller & Young
Vinyl Seals are supplied with contact adhesive on the back
1. If using the optional vinyl seals, peel the backing
off the vinyl seal and press it carefully onto the document.
2. If the paper is moistened with a wet sponge on the
back of the document within the vinyl seal area only, at this stage, this
will improve the embossing making it more permanent and require less pressure.
3. The imprint of the seal is then made combining the
two together. For best effect, Press and hold for a few seconds to
give the embossing time to set. Use a firm grip but do not overload
the press.
If the embossing is not good enough, check the following.
We recommend returning the press immediately if there is any problem as
the cause is not always obvious to the user and further use can make it
worse.
1. Paper too thick or too hard.
2. Damaged dies.
3. Dies not damaged but loose in press. Re-alignment
may be all that is required.
4. Press guides worn |
|