POWERED INDUSTRIAL TRUCK OPERATOR TRAINING
OSHA - FINAL RULE
The Occupational Safety and Health Administration (OSHA) published a final rule requiring training
of powered industrial truck operators on December 1, 1998 (63 FR 66238, 29 CFR Parts 1910, 1915, 1917, 1918 and
1926. The final rule was adopted on November 17, 1998). The new requirements apply to the use of powered industrial
trucks in general industry, construction, shipyards, marine terminals and longshoring operations. They do not apply
to agricultural operations.
In general, the rule requires employers to develop an operator training program that incorporates the basic principles
of safe truck operation for the type of trucks being used in the workplace and recognizes the hazards in the workplace.
The amount of time devoted to training and the method of training is to be determined by the operator’s demonstrated
ability to operate the truck safely. Each operator’s performance must be evaluated at least every three years and
refresher training must be provided when needed.
Summary and Explanation of the Final Rule
General
Powered industrial truck operators must be trained before they are allowed to operate the trucks independently.
The training must include both classroom-type and practical instruction in proper vehicle operation, the hazards
of operating the vehicle in the workplace and the requirements of the OSHA standard for powered industrial trucks.
After completion of training, the operator must be evaluated while operating the vehicle in the workplace. Thereafter,
operators must be evaluated periodically and receive refresher training whenever there is a demonstrated need.
Scope
The final rule applies to all powered industrial trucks defined in the voluntary consensus standards,
such as ASME B56.1 (low and high lift trucks), ASME B56.5 (guided industrial vehicles), ASME B56.6 (rough terrain
forklift trucks), and ASME B56.7 (industrial crane trucks). In addition, the rule applies to any other vehicles
that fall within the definition of powered industrial trucks in § 1910.178(a). The rule also applies to specialized
equipment found in marine cargo handling operations.
The rule does not apply to earth-moving equipment or vehicles used for over-the-road
hauling.
Safe Operation
Section 1910.178(l)(1) establishes the basic requirement for operator training.
(l) Operator training.
(1)Safe operation. (i) The employer shall ensure that each powered industrial truck operator is competent to operate
a powered industrial truck safely, as demonstrated by the successful completion of the training and evaluation
specified in this paragraph (l).
(ii) Prior to permitting an employee to operate a powered industrial truck (except for training
purposes), the employer shall ensure that each operator has successfully completed the training required by paragraph
(l)(5).
The employer has the obligation to provide training for industrial truck operators. The employer’s obligation is
to ensure that each operator is competent to operate the trucks safely, as demonstrated by the successful completion
of the training and evaluation required by the rule. Although the rule does not cover all "potential"
operators, an employee who has other duties, but sometimes operates a powered industrial truck, is covered by the
rule.
The employer may satisfy the training obligation in a number of ways. The employer may retain the services of a
qualified outside training organization to provide evidence that the employee as successfully competed the relevant
classroom and practical training topics. Alternatively, the employer may have another employee perform the training
and evaluation, which would allow the employer to certify that the employee is competent to operate the truck safely.
Lastly, the employer may not permit an employee to operate a powered industrial truck without supervision until
the required training and evaluation has been successfully completed.
Training Program Implementation
Section 1910.178(l)(2) specifies the type of training required and the qualifications of the person conducting
the training and performing the evaluations.
(2) Training program implementation.
(i) Trainees may operate a powered industrial truck only:
Under the direct supervision of persons who have the knowledge, training, and experience to train operators and
evaluate their competence; and
(B) Where such operation does not endanger the trainee or other employees.
(ii) Training shall consist of a combination of formal instruction (e.g., lecture, discussion, interactive computer
learning, video tape, written material), practical training (demonstrations performed by the trainer and practical
exercises performed by the trainee), and evaluation of the operator's performance in the workplace.
(iii) All operator training and evaluation shall be conducted by persons who have the knowledge, training, and
experience to train powered industrial truck operators and evaluate their competence.
The rule prohibits employers from allowing trainees to operate a powered industrial truck without the direct supervision
of the trainer. Training must be conducted only in areas where truck operation does not endanger the trainee or
other employees.
The training program must consist of formal instruction, practical training and an evaluation of the trainee’s
performance in the workplace. The formal training portion of the program may include lectures, discussion, interactive
computer learning, videotape and written material. Practical training must consist of demonstrations performed
by the trainer and practical exercises performed the trainee.
The trainer, whether a third-party organization or another employee, must have the knowledge, training and experience
to train and evaluate operator competence.
E. Training Program Content
Section 1910.178(l)(3) specifies the topics that must be covered in the training program.
(3) Training program content. Powered industrial truck operators shall receive initial training in the following
topics, except in topics which the employer can demonstrate are not applicable to safe operation of the truck in
the employer's workplace.
(i) Truck-related topics:
Operating instructions, warnings, and
precautions for the types of truck the operator will be authorized to operate;
(B) differences between the truck and the automobile;
(C) Truck controls and instrumentation; where they are located, what they do, and how they work;
(D) Engine or motor operation;
(E) Steering and maneuvering;
(F) Visibility (including restrictions due to loading);
(G) Fork and attachment adaptation, operation, and use limitations;
(H) Vehicle capacity;
(I) Vehicle stability;
(J) Any vehicle inspection and maintenance that the operator will be required to perform;
(K) Refueling and/or charging and recharging of batteries;
(L) Operating limitations;
(M) Any other operating instructions, warnings, or precautions listed in the operator's manual for the types of
vehicle that the employee is being trained to operate.
(ii) Workplace-related topics:
(A) Surface conditions where the vehicle will be operated;
(B) Composition of loads to be carried and load stability;
(C) Load manipulation, stacking, and unstacking;
(D) Pedestrian traffic in areas where the vehicle will be operated;
(E) Narrow aisles and other restricted places where the vehicle will be operated;
(F) Hazardous (classified) locations where the vehicle will be operated;
(G) Ramps and other sloped surfaces that could affect the vehicle's stability;
(H) Closed environments and other areas where insufficient ventilation or poor vehicle maintenance could
cause a buildup of carbon monoxide or diesel exhaust;
(I) Other unique or potentially hazardous environmental conditions in the workplace that could affect safe
operation.
(iii) The requirements of this section.
This section contains a relatively extensive list of training topics focused on the vehicle as well as the workplace.
The topics are based on those contained in the ASME B56.1 voluntary standard. While the employer is permitted to
exclude some of the topics that are not relevant to safe operation in a particular workplace, the employer bears
the burden of demonstrating that the excluded topics are not necessary. The employer’s obligation to justify exclusion
of the topics would, in normal course, arise in the context of an OSHA inspection or an investigation of an accident.
Refresher Training and Evaluation
Section 1019.178(l)(4) requires refresher training and evaluation after certain triggering events and an evaluation
of each operator’s performance at least every three years.
(4) Refresher training and evaluation.
(i)Refresher training, including an evaluation of the effectiveness of that training, shall be conducted
as required by paragraph (l)(4)(ii) to ensure that the operator has the knowledge and skills needed to operate
the powered industrial truck safely.
(ii) Refresher training in relevant topics shall be provided to the operator when:
(A) The operator has been observed to operate the vehicle in an unsafe manner;
(B) The operator has been involved in an accident or near-miss incident;
(C) The operator has received an evaluation that reveals that the operator is not operating the truck safely;
(D) The operator is assigned to drive a different type of truck; or
(E) A condition in the workplace changes in a manner that could affect safe operation of the truck.
(iii) An evaluation of each powered industrial truck operator’s performance shall be conducted
at least once every three years.
OSHA had originally proposed a requirement for annual refresher training based upon ITA’s recommendation. The final
rule requires that periodic evaluations of operator performance be conducted only once every three years. OSHA
reasoned that annual evaluations were unnecessary given the requirement for initial training, refresher training
and evaluation when necessary and periodic evaluations. The triennial evaluation could be as simple as having a
qualified individual observe the operator’s performance.
The events which trigger the requirement for refresher training are based upon the 1993 version of the ASME B56.1
voluntary standard. They are tied to the operator’s performance as well as the use of new truck types and changes
in workplace conditions.
Avoidance of Duplicative Training
To address concerns from various employer groups, OSHA provided an exception to the training requirement to avoid
duplicative training.
(5) Avoidance of duplicative training.
If an operator has previously received training in a topic specified in paragraph (l)(3) of this section, and such
training is appropriate to the truck and working conditions encountered, additional training in that topic is not
required if the operator has been evaluated and found competent to operate the truck safely.
The exception to the training requirement applies both to new hires as well as current employees. The employer
is not required to use written documentation of the operator’s prior training to determine his competence. The
employer can satisfy his obligation under this provision by conducting an evaluation of the operator’s performance.
An employer can satisfy his obligation under this provision by conducting an evaluation of the operator’s performance.
While it seems reasonable to avoid a requirement for duplicative training, the laxness of this provision is not
consistent with a commitment to strong training programs.
Certification
The final rule requires that the employer certify that each operator has been trained and to maintain a record
of the training.
(6) Certification.
The employer shall certify that each operator has been trained and evaluated as required by this paragraph (l).
The certification shall include the name of the operator, the date of the training, the date of the evaluation,
and the identity of the person(s) performing the training or evaluation.
The certification and record-keeping requirement in the proposed rule were controversial. OSHA attempted to the
need to require evidence that operators were trained and certified with employers’ desire to avoid paperwork burdens.
The result is that employers do not have to retain training materials and information from outside trainers, nor
do they have to obtain the signature of the individual who conducted the training.
Dates
(7) Dates. The employer shall ensure that operators of powered industrial trucks are trained, as appropriate,
by the dates shown in the following table.
If the employee was hired: |
Initial training must be completed: |
Before December 1, 1999 |
By December 1, 1999 |
After December 1, 1999 |
Before employee is assigned to operate a powered industrial truck |
Appendix
ITA originally requested that an appendix be published with the final rule that contained a list of
training topics. OSHA decided not to include the requested appendix because most of the items were incorporated
in the rule itself. In the final rule, OSHA included a non-mandatory appendix that provides guidance to employers
and employees on the basic principles of truck stability.
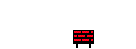
FORKLIFT OPERATION AND SERVICE.
BE SURE TO VISIT THE HOME PAGE FOR INFORMATION ON LIFT TRUCKS REPAIR, SERVICE, TROUBLESHOOTING,
AND EVERYTHING YOU NEED TO KNOW ABOUT FORKLIFTS AND THEIR USE.
|