What type of navigation or guidance system should
you choose to control AGV traffic?
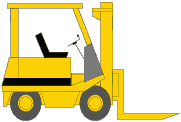
EVERYTHING AN OPERATOR AND MECHANIC NEEDS
TO KNOW ABOUT FORKLIFTS AND LIFT TRUCKS.
HELPFUL INFORMATION ON FORKLIFT AND LIFT TRUCK OPERATION, SERVICE,REPAIRS,TROUBLESHOOTING, MAINTANCE, OPERATOR'S
USE, BATTERY MAINTANCE AND A LITTLE OF EVERYTHING TO KEEP A FORKLIFT RUNNING.
What type of navigation or guidance system should you choose to control AGV traffic and track vehicle locations
in your potential materials handling application?
You can select from among a half dozen guidance options These systems instruct vehicles to follow either a fixed
path or an open path.
AGV technology began with the fixed path systems. Updated versions of these systems are still installed today,
however. The AGVs follow a well-marked, continuous path, which is either on or buried within the floor. But users
sacrifice some flexibility should business requirements change. New needs mean new paths. The user must add to
existing pathways and perhaps uninstall or wipe out old pathways.
In contrast, open path systems give AGVs more freedom to roam, within prescribed limits, about the plant. Users
get more flexibility.
Fixed path methods.
Guidance by these systems requires either (1) creating a pathway on the floor surface or (2) burying a wire just
below the surface.
Applying a narrow magnetic tape, a photo sensitive chemical strip, or a photo reflective tape to the floor surface
are among the established techniques for creating above-surface pathways. These optical systems require use of
a sensor on the underside of the vehicle to detect the pathway. If the sensor comes upon a turn in the pathway,
it senses that fact and then sends instructions to an onboard controller to steer the AGV through the turn.
Similarly, in buried wire systems an under vehicle sensor detects a magnetic field created by current flow in the
wires. The AGV follows the path by sensing differences in signal strength and frequency. And, depending upon whether
the vehicle is centered over the buried wires or is off center, to the left or right, the AGV makes needed course
corrections.
Navigation by fixed path systems is by the shortest distance between points A and B or is by the path where the
least traffic is expected at a point in time, in general.
Open path methods.
In many AGV systems installed recently, the guidance method selected is by open systems. They offer more inherent
flexibility than do the fixed methods. Vehicles operate in a "take a path" mode rather than a "follow
a path" mode. Thus, the vehicles have far more, if not necessarily infinite, variability in the ways they
cover the distance between points A and B.
What these open systems require are two things: (1) a map of the AGVS operating area and (2) multiple, fixed location
reference points which can be detected or "seen" by the AGVs. Vehicles need to know where they are exactly
and then be able to take a directional heading to where they want to go.
This area map is stored in system memory at a central point and in computers onboard the vehicles. The different
open path guidance methods then give their AGVs the location reference data through one or more techniques:
Laser-guided vehicles get their "map" reference points by data returned from a vehicle mounted, rotating
laser scanner beam. This beam detects passive reflective targets affixed vertically to walls and columns within
the facility. With detection of only 2 targets, or more ideally of 3 targets, the system determines location and
heading by simple geometry.
Inertially-guided vehicles have an onboard gyroscope to determine and maintain heading. Through onboard odometry,
such as counting wheel rotations, the AGV calculates distances traveled. Many AGV systems using this combination
of gyroscopic data and vehicle odometry go one step further: They achieve high precision in vehicle location by
an under vehicle sensor detecting magnets or transponders embedded into the floor.
Cartesian guidance
for vehicles involves determining an AGV’s location by sensing its specific position coordinates of X and Y as
the vehicle operates over a grid pattern on the floor. Odometry also is necessary in these systems. And in larger
vehicles there may be an onboard gyroscope for navigation.
Modern Materials Handling 01/01/2001
THANK YOU AND I HOPE YOU ENJOY MY PAGE.
|